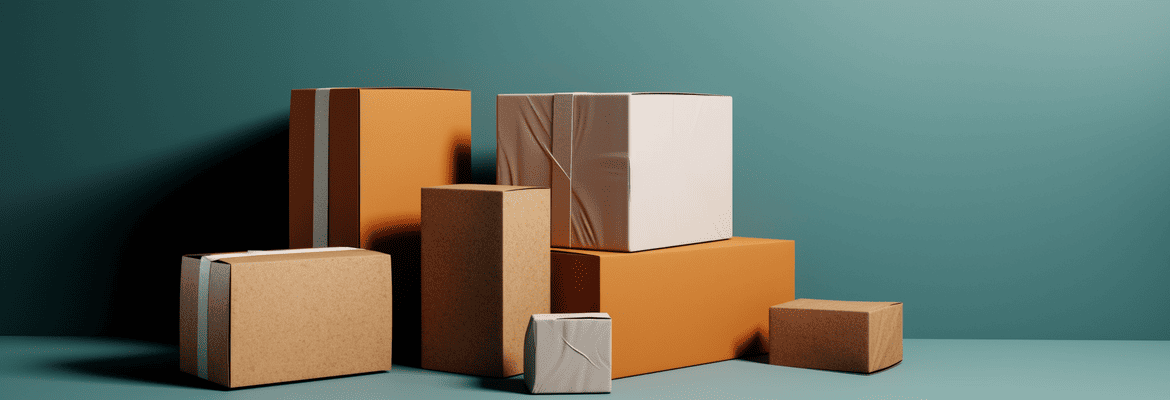

Technical terms explained: Packaged goods
Packaged goods is the term used to describe the goods that are packaged and, if necessary, shipped. It is divided into seven different categories, which also reflect the respective specific properties. These in turn are relevant for choosing the appropriate packaging.
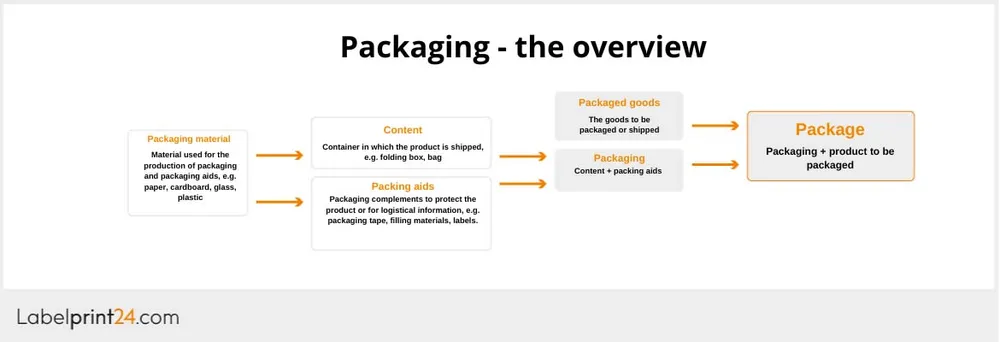
Packaged goods - definition, categories, explanations of terms
Products are usually transported, stored, delivered and finally offered for sale in suitable packaging. Packaged goods are goods that are already packaged or that still need to be packaged. They have product-specific properties.
These properties in turn result in special requirements for the packaging. Relevant criteria are, for example, the type of packaged goods, its consistency and weight as well as the requirements regarding storage. The packaging must therefore fit the respective packaged goods in terms of material, size and shape.
The properties of the packaged goods determine the packaging material
Depending on the packaged goods, different packaging materials are used. Typical examples are
- Boxes,
- cardboard boxes,
- bags,
- Blisters (visible packaging),
- boxes,
- glass containers and
- film packaging
Which packaging material is best suited depends largely on the category to which the respective packaged goods belong. For example, products from the category of flowable goods generally require printed packaging made of more stable and stronger material than unit loads with a higher inherent stability.
Different packaged goods categories
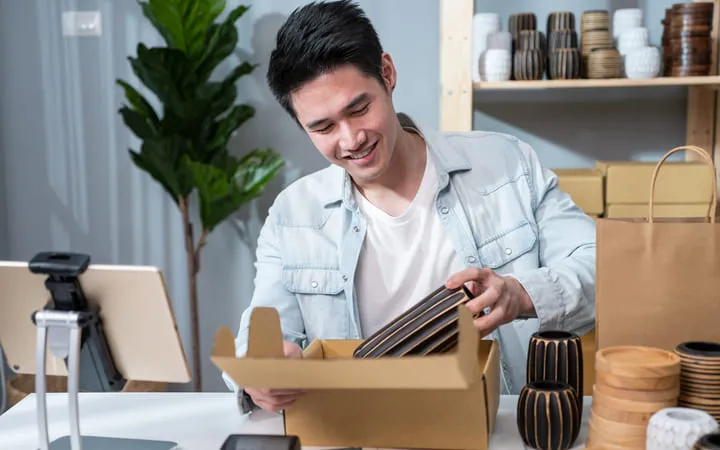
General cargo
These are product units that are stored or transported individually. These include, for example, books, assembly parts, pieces of furniture, machines or clothing.
A general cargo does not necessarily have to be a single package - a pallet filled with goods, a crate or a barrel can also constitute a packaged good. In order to be declared as a general cargo, these three conditions must generally be met:
- it is not a flowable or bulk good
- can be transported individually in one piece
- has a fixed aggregate state or a fixed geometric shape
Grouped goods
The term describes a bundling of general cargo. This can involve both identical and different unit loads. Packing aids combine smaller units into a larger transport or delivery unit. By combining several deliveries, transport can be optimised in this way.
The bundled general cargo can be of the same or different type and nature. Grouped goods as a bundling of several general cargoes offer several advantages:
- optimised use of resources
- cost savings
- better and more efficient transport and delivery routes
- Environmentally friendly transport due to reduced distances
However, a good organisational structure as well as a supra-regional network are necessary to put together a groupage of several general cargoes. In addition, the planning is comparatively error-prone and there may be delays in bundling the general cargo.
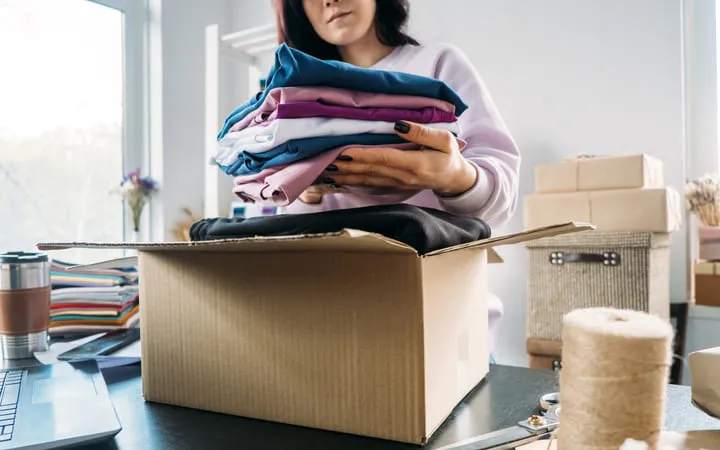
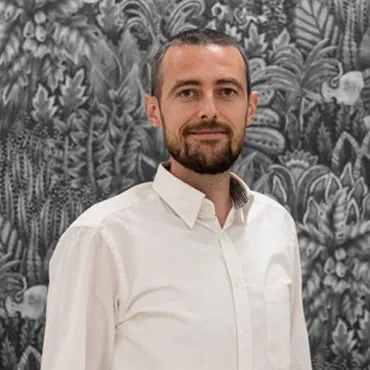
Product Advisor for Shipping Boxes
Whether it’s a simple folding box or a maxi letter box with adhesive strips – I’m your advisor for shipping boxes made from corrugated cardboard. Our printed packaging and inlays provide protection for products across almost all industries.
"Security and design? Corrugated cardboard offers both!"
I will be happy to help you personally.
Filling goods
This term describes substances that are filled into bags, containers or similar packaging materials. Typical filling goods are, for example, milk, rice, shampoos or washing-up liquid. If the respective contents are in a liquid state, a packaging must be chosen that prevents any potential interaction with the contents.
If the contents contain harmful substances, they must be treated separately. In this case, the filling is carried out in packaging specified for this purpose.
Flowing and bulk goods
In freight transport, products are referred to as flowing goods if they do not have a fixed geometrically defined shape. This is the case, for example, with liquids and products with a viscous consistency, but also with bulk goods such as sand, chippings or gravel.
Goods containing harmful substances
According to the Packaging Act (VerpackG), for example, pest control substances, plant protection agents, polyurethane foams, and certain other chemicals or chemical-containing products, as well as fuels, oils, and oil-based products (lubricating oil, brake fluid, etc.), are considered hazardous contents. They must be labeled with appropriate hazard symbols or GHS pictograms.
Dangerous goods
Goods of this type have special requirements with regard to safe packaging, transport and storage. The term dangerous goods covers all substances that may pose a risk to the health and life of people and thus also to public safety. Here, too, requirements apply to labelling, e.g. with labels. The transport of dangerous goods is strictly regulated by law. These primarily relate to transport in public traffic. Other rules apply to the transport of dangerous goods within closed company premises.
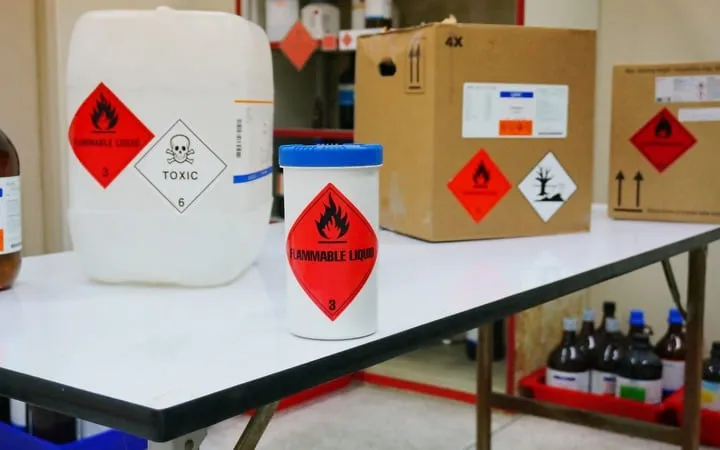
In general, the following packaged goods, among others, belong to the category of dangerous goods:
- Fireworks
- ammunition and explosives
- radioactive substances
- toxic and infectious substances
- substances hazardous to water and the environment
- oxidising substances
- spontaneously combustible and flammable solids, liquids, gases and gas mixtures
Dangerous goods can be divided into three differently defined packaging groups: substances with low, medium and high hazard potential.
The right packaging solution for every packaged good
Poorly and not carefully packed products can be damaged more easily. This can lead to considerable additional costs on the one hand and also to a loss of image on the other. The company department responsible for packing goods or the responsible packaging service provider must therefore ensure that the goods arrive undamaged at the recipient.
For this reason, they must find increasingly product-specific solutions with regard to the shape, construction and material of the packaging e.g. custom-made cartons. This ensures the best possible protection for the respective packaged goods. The development of new packaging solutions and the most individual design options possible are also high on the agenda here.
The most important tasks in handling packaged goods
The handling of packaged goods must always be carried out according to the specifications.
- The integrity and quality of the packaged goods must be guaranteed at all times.
- The maximum packaging volume must be specifically designed for the respective package.
- Packaged goods should not have any protruding elements in order to prevent potential hazards to people or other goods.
- Easily destructible or fragile packaged goods must be secured separately.
- Substances hazardous to water and the environment
- Each packaged good must be assessed on the basis of its individual specification. Depending on the requirements, packaging service providers must implement protection against electrostatic discharge or corrosion, for example.
Particularly in the case of dangerous goods, special laws and regulations also come into play. In Germany, the handling of packaged goods in this category is regulated in the Dangerous Goods Ordinance for Road, Rail and Inland Navigation (GGVSEB). Among other things, this results in obligations with regard to dispatch, transport, packaging and loading and unloading.
Selecting packaging solutions that match the packaged goods
When it comes to finding the right packaging for a product, it all depends on its properties. Liquids, for example, are packed in different packaging than products with a solid body.
The number and variety of packaging is now very large. There is an explicitly designed packaging solution for every type of packaged good. The following typical examples show various details and product variants - for an optimal symbiosis of packaged goods and packaging:
Stand-up pouches made of a film composite (PET/EVOH/PE) with a high aroma, oxygen and moisture barrier for food in the form of pastes, powders or liquids. Resealabe variants can also have a positive effect on the shelf life of the packaged goods.
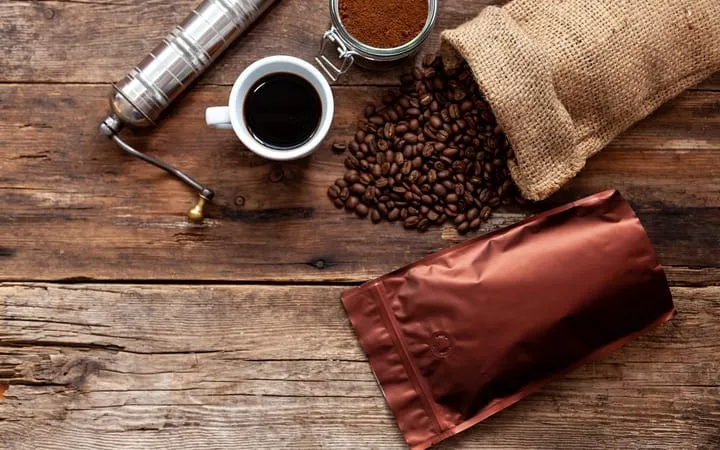
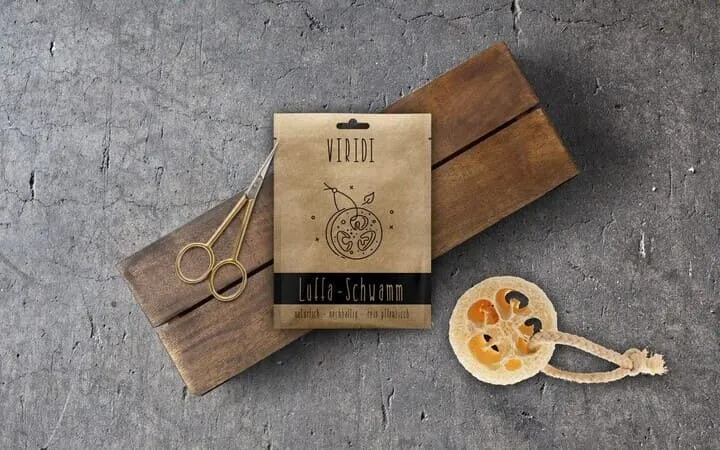
Particularly tear-resistant and sealed flat bags without bottom made of polypropylene and polyethylene for the hanging or lying presentation of packaged goods at the point of sale using Euro hole hangers. These include, for example, cosmetics, screws and other small parts as well as food and luxury foodstuffs.
Folding cartons made of double wall corrugated board for heavier packaged goods weighing up to 32 kg.
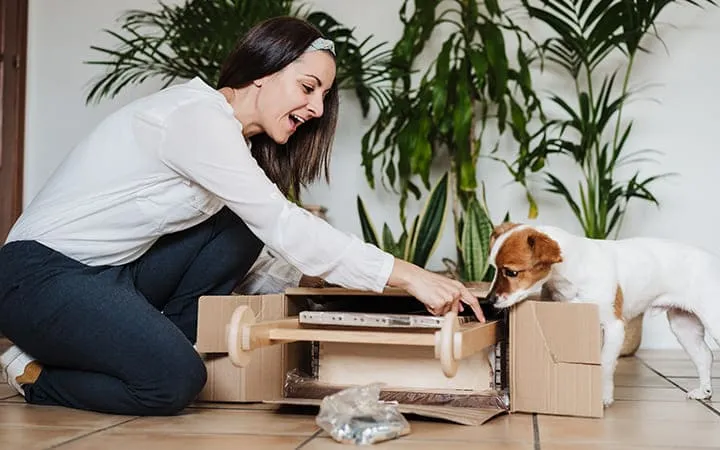
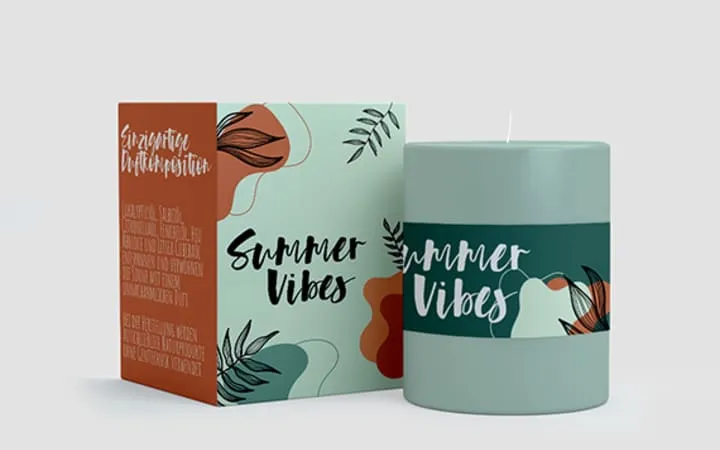
Folding boxes with tuck-in bottom made of recyclable and compostable cellulose board with high tear strength and flexural rigidity for protective and stylish packaging of packaged goods such as cosmetics and pharmaceutical products.
Packaged goods and the sustainability factor
High demands are also placed on packaged goods in terms of climate and environmental protection as well as sustainability. For the commercial market players as well as for the end consumers, this topic is more in focus than ever before. Therefore, packaging professionals must present suitable solutions accordingly and focus on resource- and energy-efficient manufacturing processes. In the context of production, packaging and transport, there are many possible approaches to reduce the consumption of energy and resources such as water and raw materials (e.g. wood) as well as pollutant emissions.
An essential step is the choice of material. Which is the most sustainable packaging solution depends on various factors - the necessary protection, possible material cycle structures (deposit systems) or even the type and length of the transport route.
- A good example of an environmentally friendly material is wood or wood fibers, from which cardboard, paper and paperboard are made. This naturally renewable raw material is CO2-neutral and can be easily recycled. Wood that comes from sustainable forestry is best.
- Corrugated board is particularly sustainable in this context. It consists largely of recycled material and otherwise of fresh fibers (broken and thinned wood). In addition, the material is almost completely recyclable.
- Grass is similar to wood: this raw material grows back quickly, is available regionally and is suitable for the production of cardboard and paper.
- A sustainable alternative to conventional, petroleum-based plastic is that made from cellophane. This material is made exclusively of wood. Uncoated, it is biodegradable and compostable.
- Recycled polyethylene terephthalate (rPET) is obtained from melted-down PET waste. Processed into granules, it can be used to produce a wide variety of things.
- Adhesives are often needed to ensure that the materials hold together well in the production of packaging. The sustainable variant is produced from plant starch.
In addition to the choice of material, the use of renewable energy sources to generate electricity during operation also contributes to the lowest possible ecological footprint. The same applies to the design of the packaging.
Quality controls - the basis for continuous improvement
The aim is also always to avoid superfluous waste. This is achieved by using packaging materials that are tailored to the goods to be packaged. This can be well illustrated by the example of cartons: The better the dimensions of a shipping carton fit the packaged goods, the less packaging and filling material is needed. Inlays for packaging are, of course, ideal.
Likewise, precisely fitting inlays help to ensure that significantly less filling material, or even none at all, is used - and that less packaging waste is therefore generated.
Packaging service providers should also introduce quality controls to check sustainability or compliance with sustainability in all respects.
This starts with checking where the raw materials used come from and how environmentally friendly they are. For recycled materials, it also matters that the source material is sustainable as well. Likewise, packaging service providers can put their resource energy consumption to the test via regular checks and measurements, to name another example.
This provides insights and a basis for optimization throughout the entire packaging process.
Conclusion: Research and development bring dynamism to the packaging industry
Every day, there are vast quantities of packaged goods that have to be transported or delivered appropriately packaged. At the same time, this results in an increasing volume of packaging waste. Added to this - depending on the material - is the sometimes very high consumption of energy and resources. By combining packaged goods into consolidated goods, a corresponding reduction and greater efficiency can be achieved.
Modern production facilities make it possible for packaging solutions to be highly individualized and adapted precisely to the respective requirement. This applies, for example, to the dimensions, optional printing and selectable finishes. Accompanying quality controls ensure compliance with specifications for the product and material cycle.
In principle, recyclable materials are also pushing more and more into the foreground. Many types of plastic are also recyclable - but not all. For functional reasons, however, they still represent an important factor as packaging materials. The challenge here is to establish new packaging materials that are much more easily degradable.
The latest developments clearly indicate that packaged goods will also be wrapped in smart packaging in the future. For example, research is underway into smart fibers that could replace classic plastic film in the long term.