

Wellpappe - die Herstellung des Kartonagen-Materials
Grundsätzlich werden die verschiedenen Wellpappearten nach der Anzahl ihrer Wellenlagen eingeteilt. Ihre spezifische Codierung gibt die Anzahl der Wellen und den jeweiligen Wellentyp an. Während die benötigten Rohstoffe zur Herstellung von Wellpappe mit drei Komponenten simpel wirken, ist der Herstellungsprozess selbst eine komplexe Angelegenheit.
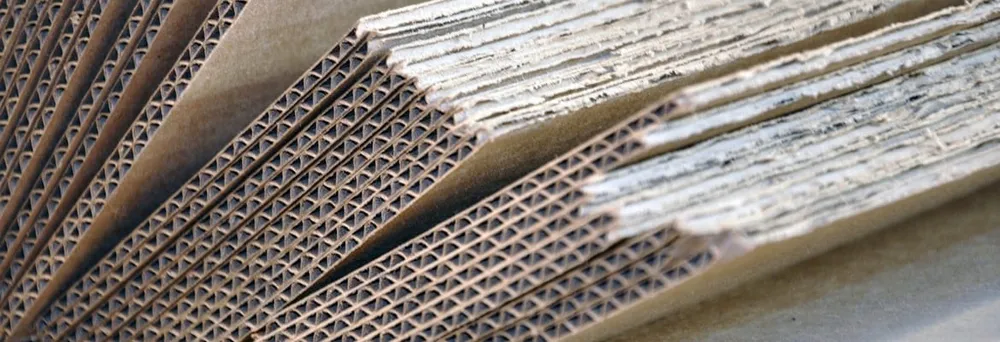
Der Aufbau von Wellpappe
Als multifunktionale Verpackung ist Wellpappe als Material für verschiedenste Kartonagen längst unverzichtbar für das Verpackungswesen. Sie überzeugt mit einem geringen Eigengewicht, einer hervorragenden Stabilität, einer nachhaltigen Herstellung und vergleichsweise günstigen Anschaffungskosten.
Wellpappe besteht dabei immer aus einer Innendecke, der Welle und einer Außendecke. Die letztendliche Stabilität einer Verpackung aus Wellpappe wird dabei in erster Linie von der Wellenart bestimmt. Entscheiden können sich die Kunden von Labelprint24 zwischen einer einwelligen und zweiwelligen Variante.
- Einwellige Wellpappe besteht aus einer inneren und äußeren Papierbahn (Innen- und Außendecken) sowie einer Welle. Alternativ gibt es einseitig beklebte Wellpappe, die sich aus nur einer Deckenbahn und einer Wellenbahn zusammensetzt.
- Zweiwellige Wellpappe basiert demgegenüber auf drei glatten Papierbahnen und zwei Wellenbahnen. Dabei werden häufig zwei verschiedene Wellenarten verwendet, die dann durch eine zusätzliche Papierbahn als Zwischendecke voneinander getrennt werden. Meistens kombinieren die Hersteller eine gröbere mit einer feineren Welle.
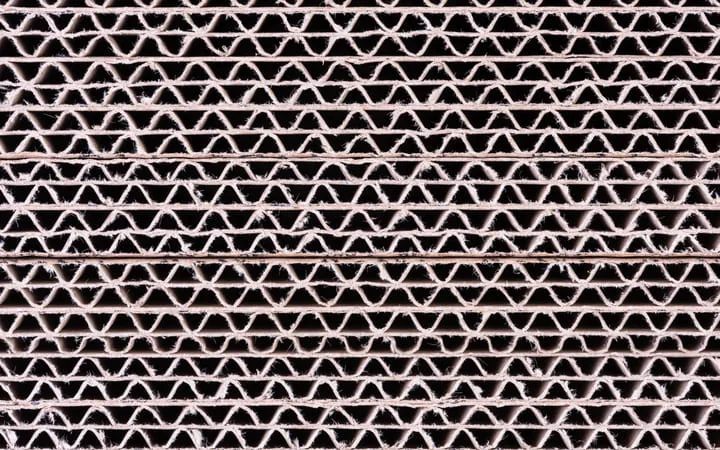
Explizite Codierungen stehen für Wellenart und Flächenlast
Um welche Wellpappenart es sich jeweils handelt, kann an bestimmten Zahlenkombinationen abgelesen werden. In den folgenden Beispielen gibt die erste Zahl die Anzahl der Wellen und die damit zusammenhängende Flächenlast bzw. Tragkraft an. Der jeweilige Wellentyp wird am Code-Ende dann in Buchstabenform dargestellt. In der Praxis stellt dies eine typische Codierung dar:
- 1.10 E steht für eine Mikrowelle mit einer Stärke von ca. 1,5 mm und einer Flächenlast von rund 10 kg.
- 1.20 B steht für eine Feinwelle mit einer Stärke von ca. 3,0 mm und einer Flächenlast von rund 20 kg.
- 1.30 C steht für eine Grobwelle mit einer Stärke von ca. 4,0 mm und einer Flächenlast von rund 40 kg.
- 2.20 EB steht für eine Doppelwelle mit einer Stärke von ca. 4,5 mm und einer Flächenlast von rund 20 kg.
- 2.50 BC steht für eine Doppelwelle mit einer Stärke von ca. 7,0 mm und einer Flächenlast von rund 50 kg.
Rohstoffe für den Herstellungsprozess
Wellpappe gilt als sehr umweltfreundlich und lässt sich besonders nachhaltig produzieren. Wellpappenrohpapier bildet dabei die Basis der Herstellung. In der Regel besteht dieses Rohpapier zu rund 80 Prozent aus Recyclingmaterialien wie zum Beispiel gebrauchtes Altpapier, Kartons und Wellpappe, die für das Recycling verwendet werden.
Hinzu kommen dann noch die sogenannten Frischfasern. Diese gewinnen die Papierfabriken aus Bruch- und Durchforstungsholz, das aus nachhaltig bewirtschafteten Wäldern stammt.
Auch der benötigte Klebstoff für die Fertigung von Wellpappe stammt direkt aus der Natur. So wird der Leim für das Verbinden der innen liegenden Wellenbahnen mit den äußeren Deckbahnen zum Beispiel aus Kartoffeln, Weizen oder Mais gewonnen. Mehr Rohstoffe bzw. Ressourcen werden für den Herstellungsprozess nicht benötigt. Aus diesem Grund gilt Wellpappe als ein nachhaltiger Packstoff.
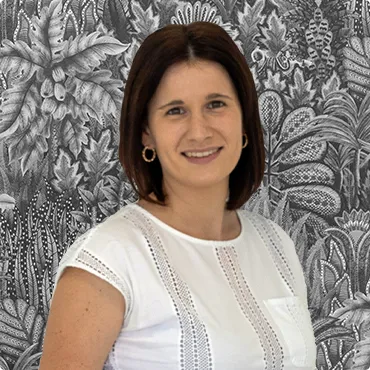


Haben Sie Fragen zu hochwertig bedruckten Versandkartons?
Ich helfe Ihnen gerne persönlich weiter.
Entdecken Sie unser Angebot an Kartonagen aus Wellpappe!
Die maschinelle Herstellung von Wellpappe
Für die Wellpappenproduktion werden Wellpappenanlagen (WPA) benötigt. Hierbei handelt es sich um eine Zusammenführung verschiedener Anlageteile im Baukastensystem.
Ein solches System erfordert sehr hohe Anforderungen im Hinblick auf die Befeuchtung, die Regulierung der Hitze, den Trockenvorgang sowie das Abkühlen. Im Groben kann die WPA dabei in Nasspartie und Trockenpartie eingeteilt werden.
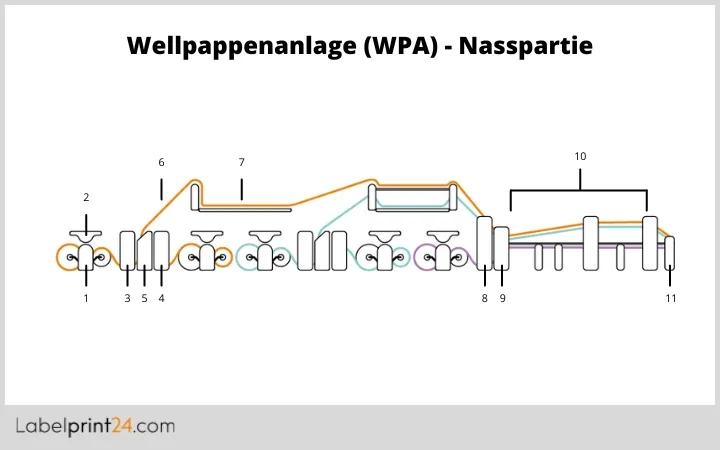
Die Nasspartie beinhaltet dabei:
- das Prägen der Wellenbahn
- das Aufbringen von Klebstoff-Verteilung
- das Verkleben von Decken- und Wellenbahnen
(1) Abrollständer (2) Splicer (3) Vorheizer (4) Vorbereiter (5)
Wellenaggregat (6) Hochtransport (7 ) Brücke ( 8 ) Vorheizzylinder
(9) Beklebemaschine (10) Heiz- und Zugpartie (11) Kurzquerschneider
Die Trockenpartie weist folgenden Produktionsverlauf auf:
- Kurzquerschneider (11)
- Rill- und Schneidaggregat (12)
- Querschneider (13)
- Ablage (14)
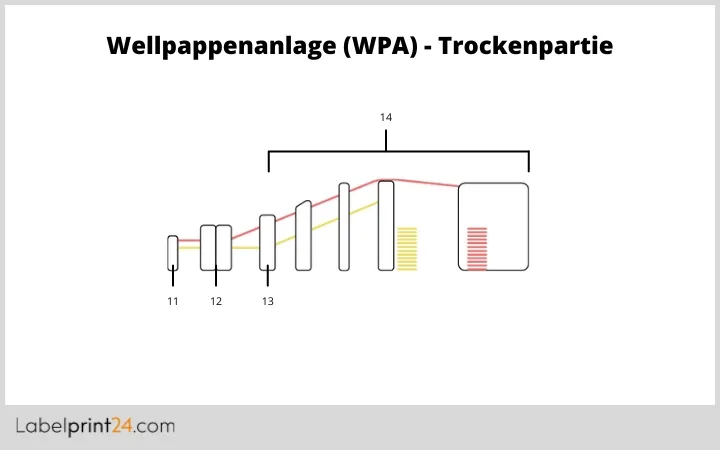
Wellpappenanlagen und ihre einzelnen Komponenten – Aufbau und Funktionsweise
1. Abrollständer
Für das faltenfreie Einlaufen bzw. Einziehen der befeuchteten Papierbahnen in die Wellpappenanlage sorgt ein achsloser Abrollständer. Die Papierrolle ist dabei nicht auf einer Achse montiert, sondern hängt mit der Hülse an zwei beidseitig angebrachten Dornen. Die Bahnspannung kann durch die rechts und links angeordneten Bremsen wunschgemäß reguliert werden.
2. Splicer
Hierbei handelt es sich um eine Vorrichtung zum automatischen Verkleben zweier Papierbahnen. Bei älteren Maschinen fehlt diese Konstruktion zwar in den meisten Fällen, aber in Anlagen moderner Prägung zählt eine Splice-Einrichtung längst zum Standard.
Der Name leitet sich dabei vom englischen „to splice“ ab. Dieser Begriff stellt einen seemännischen Fachausdruck für das Entflechten einer Öse oder das Verbinden von Tauen dar.
Von der Funktionsweise her läuft auf der einen Seite des Abrollständers noch die aktuell verarbeitete Papierbahn, während gleichzeitig auf der gegenüberliegenden Seite eine neue Rolle vorbereitet wird.
Dazu zieht eine Walze den Anfang der Papierbahn in die Klebevorrichtung der Maschine. Das Papier wird dann über ein Vakuum angesaugt und mit einem beidseitig haftenden Klebeband versehen. Anschließend führt die Maschine den Anfang der neuen Rolle an die noch aktuell ablaufende Maschine heran. Der Wechsel der Rollen zum richtigen Zeitpunkt erfolgt automatisch, kann aber auch manuell per Tastendruck ausgelöst werden.
3. Vorheizer
Im Rahmen der dritten Prozessstufe werden die Bahnen vor dem Klebevorgang noch einmal aufgewärmt. Bei den meisten Maschinen funktioniert das, indem die Papierbahn einen dampfbeheizten Zylinder in der Form eines so bezeichneten Vorheizers umschlingt. Der Durchmesser des Zylinders liegt in der Regel bei rund 80 cm. Die Erwärmung der Papierbahnen beschleunigt den späteren Klebeprozess.
4. Vorbereiter
Im nächsten Schritt wird ein Prägevorgang gestartet, der die Formbarkeit und Elastizität des Papiers sicherstellt. Bei diesem Prägevorgang werden die Verformung und Elastizität durch Wasserdampf (Feuchtigkeit) und Hitze unterstützt. Dafür läuft die Wellenbahn über den so bezeichneten Vorbereiter.
Hierbei handelt es sich vorzugsweise um einen etwa 60 cm großen, drehbaren Heizzylinder mit einer zusätzlichen Vorrichtung zur Befeuchtung. Alternativ verfügen einige Maschinen über Heizplatten oder beheizbare Walzen. Auch in diesem Fall umschlingen die Papierbahnen den Zylinder, Heizplatten oder Walzen.
Die Temperatur lässt sich dabei regeln bzw. steuern, indem die Länge der jeweiligen Umschlingung verändert wird. Der Wasserdampf weist eine Temperatur von ca. 180 °C auf. Die Mehrzahl der Wellpappenfabriken erzeugen den Wasserdampf selbst.
5. Wellenaggregat
Anschließend erzeugt die Wellpappenanlage über die im System integrierten Wellenaggregate die für die Wellpappe typische Riffelung. Dabei kommen zwei Riffelwalzen zum Einsatz, wobei zumindest eine der beiden Walzen beheizt ist.
Beide Walzen verfügen dabei über entsprechende Ausprägungen für die Riffelung der Papier- bzw. Wellenbahn. Um eine einwandfreie Prägung des Wellenpapiers zu gewährleisten, muss das Papier über eine stets hohe Formbarkeit, Elastizität und Zugfestigkeit verfügen.
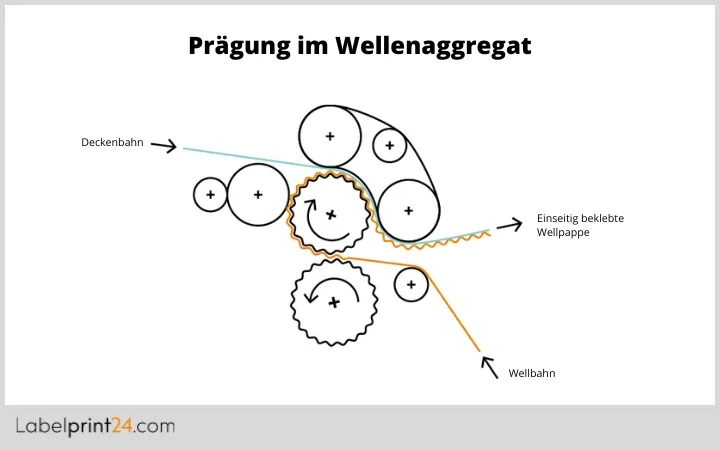
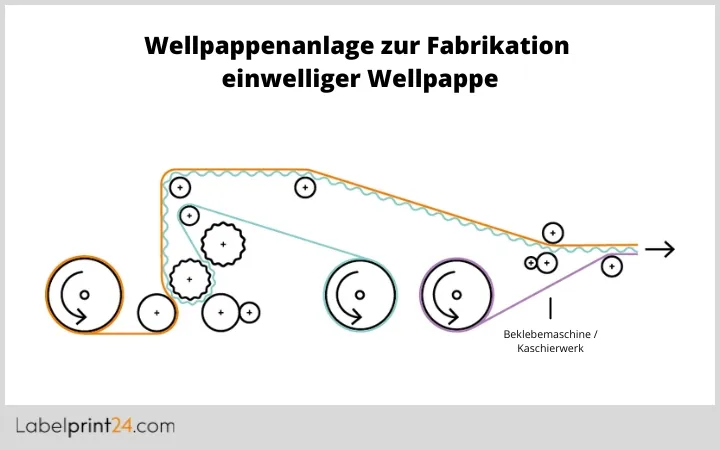
6. Kaschierleimwerk
Ist die Prägung der Welle abgeschlossen, verklebt die Maschine im nächsten Prozessschritt die Wellenbahn mit der Deckenbahn. Das passiert im sogenannten Kaschierleimwerk. Dieses ist für jede einseitige Bahn mit einzelnen Modulen ausgestattet.
Zu Beginn des Leimvorgangs werden erst die Wellenspitzen benetzt, bevor das automatisierte Auftragen des Klebstoffs von der sich drehenden Leimauftragswalze erfolgt. Zuvor taucht die Walze in den Klebstoff ein.
Das Kaschierleimwerk verfügt zudem über verschiedene Tools zur Optimierung der Klebstoff-Verteilung. So kommt eine rotierende Rakel oder eine Abquetschwalze zum Einsatz, um den möglicherweise ungleichmäßig aufgenommenen Klebstofffilm zu glätten.
Der Gelierpunkt, also die Temperatur beim Verkleben der Bahnen, liegt im Normalfall zwischen 55 und 60 °C. Die Verklebung selbst führt meistens eine in der Anlage integrierte Bandmaschine oder Presswalzenmaschine durch.
7. Heiz- und Zugpartie
Im Anschluss an den Leimauftrag auf die einseitig beklebte Wellpappe werden die Außenbahnen und die geriffelte Wellpappenbahn dann wieder zusammengeführt. Dies erfolgt gerade bei vielen älteren Maschinen über Führungsschienen. Gemeinsam durchlaufen die verschiedenen Bahnen dann die Heiz- und Zugpartie.
Das Verkleben der Bahnen mit der Außendecke geschieht dabei grundsätzlich im Rahmen der Heizpartie. Die einzelnen Bahnen werden sowohl miteinander als auch mit der Außendecke bzw. der Außenbahn verklebt. Die dafür erforderliche Wärme erzeugen beheizte Platten, die unterhalb der Außendecke platziert sind. Dabei geht die Wärme durch die glatte Außenbahn zu den Klebestellen.
Dieser Vorgang ist technologisch sehr anspruchsvoll. Besteht beim Verkleben zum Beispiel ein zu hoher Druck, würde das die Wellpappe deformieren und letztendlich auch die Festigkeit und Stabilität reduzieren. Daher muss die Wärmeübertragung mithilfe von verschiedenen Systemen gesichert werden, indem die Wellpappen vorsichtig und schonend auf die Heizplatten gedrückt werden. Je nach Konstruktion der Wellpappenanlage stehen hier verschiedene Systeme zur Verfügung.
Besonders relevant sind diese drei Systeme:
- das Luftkissensystem
- das Beschwerwalzensystem
- Gleitketten oder Gleitschuhe
Demgegenüber ist die so bezeichnete Zugpartie für den Transport der Wellpappe bzw. der Bahnen durch die Beklebemaschine und anschließend durch die Heizpartie verantwortlich. Die Wellpappe wird für den Transport zwischen einem Obergurt und einem Untergurt fixiert. Um diese Konstruktion in der Maschine zu bewegen, sind enorme Kräfte notwendig. Walzen drücken die Gurte zusätzlich aneinander, was einen hohen Reibwiderstand erzeugt.
Insbesondere bei hohen Produktionsgeschwindigkeiten können auf diese Weise Beschädigungen der Wellpappe verringert werden. Modernere Anlagen sind inzwischen oftmals mit einem Vakuum-Untergurtsystem ausgestattet. Ein solches System macht den Obergurt überflüssig und verringert dadurch den Anpressdruck, was die Gefahr von Schäden an der Wellpappe noch weiter minimiert.
8. Kurzquerschneider
Genau zwei Aufgaben muss der Kurzquerschneider erfüllen: Zum einen dient er dazu, mangel- und fehlerhaftes Material, das aus der Nasspartie kommt, herauszuschneiden. Zum anderen durchtrennt das Werkzeug die Papierbahn bei einem Format- oder Auftragswechsel.
Das ermöglicht es im Hinblick auf den neuen Auftrag, die nachfolgenden Rill- und Schneidwerkzeuge entsprechend den Anforderungen zu wechseln. Die Produktionsgeschwindigkeit muss hierfür in der Regel nicht reduziert werden. Der Werkzeug-Wechsel findet bei laufender Maschine statt.
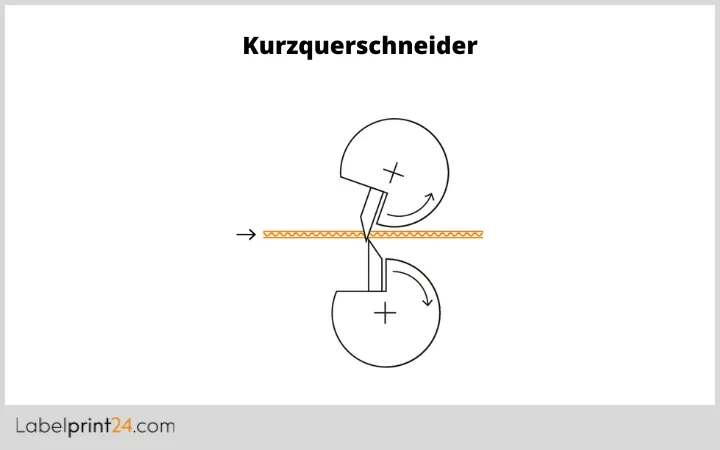
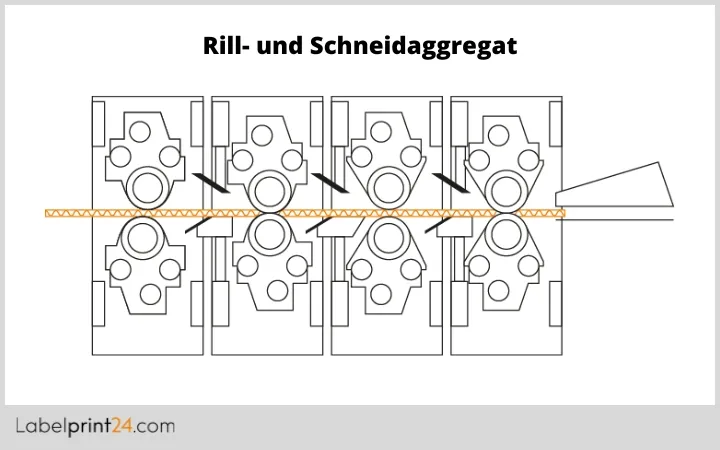
9. Rill- und Schneidaggregat
Die immer noch endlos belassene Wellpappenbahn wird in der nächsten Station gerillt und längs geschnitten. Zum Einsatz kommen dabei spezifische Rill- und Schneidwerkzeuge.
Wo genau die Werkzeuge positioniert werden, ist dabei immer abhängig von den später beim fertigen Produkt gewünschten Klappenlängen und Höhenabmessungen. Bei der Bearbeitung durch die Rill- und Schneidwerkzeuge liegt die Welle bei den gängigen Maschinentypen immer quer zur Wellenbahn. Die Rillung bzw. Rilllinien befinden sich dabei parallel zu den Schnittlinien.
Die endlose Papier- bzw. Pappbahn wird von dem Rill- und Schneidaggregat dann in Längsrichtung geteilt. Dadurch sind die Schnitte immer quer zur Welle platziert. Für die Bearbeitung stehen viele verschiedene Profilformen zur Verfügung. Einige Wellpappen-Hersteller haben sogar eigene Profile entwickelt. Besonders häufig kommen dabei Tellermesser zum Einsatz, die wie eine rotierende Schere funktionieren.
10. Querschneider
Der so bezeichnete Querschneider folgt in der Prozesskette direkt auf das Rill- und Schneidaggregat. Hier geht es um das Zuschneiden der Bogenlänge (fachspezifisch auch Haulänge genannt). Der Querschneider trennt mit seinen Ober- und Untermessern die Endlos-Bahnen immer parallel zum Wellenverlauf respektive quer zur Laufrichtung. Angetrieben werden die Messer dabei von elektronisch gesteuerten Elektromotoren.
Viele Wellpappenanlagen sind mit mindestens zwei unabhängig voneinander arbeitenden Querschneidern ausgestattet. Das wird als Duplex bezeichnet. Es gibt außerdem Maschinen mit drei autark funktionierenden Querschneidern ( Triplex). Duplex- und Triplex-Querschneider erhöhen dabei die Kombinationsmöglichkeiten für optimale Schnittlisten.
11. Ablage
Die einzelnen Bogen werden dann nach der Arbeit der Querschneider jeweils schuppenförmig auf Fördergurte abgelegt und anschließend stapelweise auf Rollbahnen abgesetzt. Wie hoch der Stapel maximal sein darf, kann individuell eingestellt werden.
Der gesamte Arbeitsprozess vom faltenfreien Einlaufen der Papierbahnen bis zum Stapeln der fertigen Produkte aus Wellpappe läuft – je nach Anlagentyp – mit einer Geschwindigkeit von bis zu 400 m in der Minute ab.