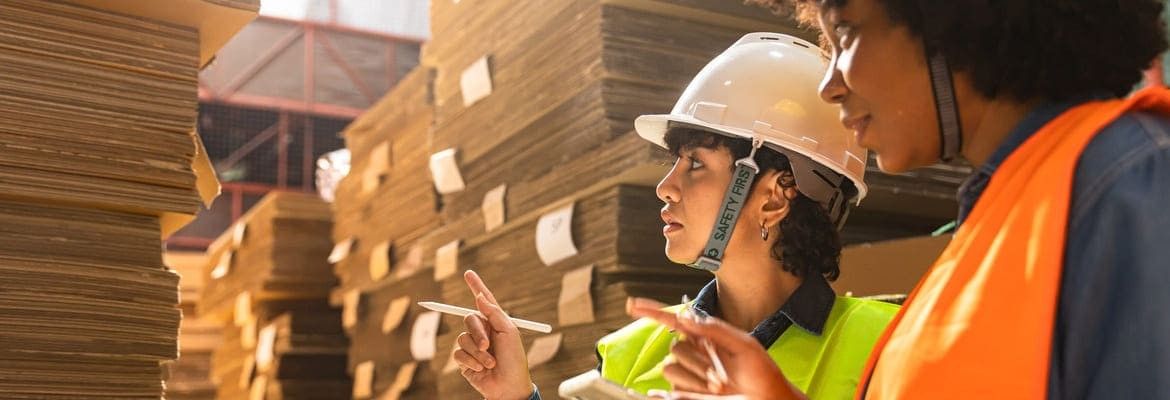

Technical terms explained: What does creasing mean?
Creasing is an important process in the packaging industry. Paper or cardboard materials are given a defined, linear notch by creasing. The material can then be folded more easily along the creasing.
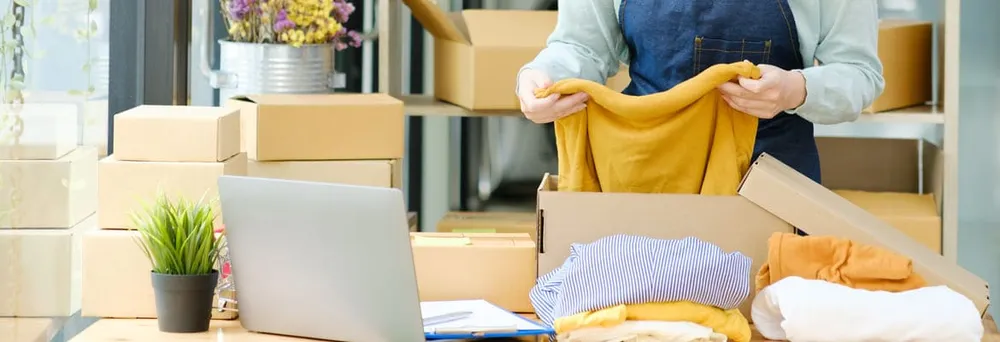
Definition of the term creasing
Creasing results from a technical process in which grooves or notches are mechanically introduced into material containing paper or cardboard. In this way, folding cartons, for example, can be folded more easily and precisely at the predefined points. If creases are made in cardboard or paperboard, this is usually for the purpose of later producing a folded edge by folding.
Without careful creasing, it is difficult to achieve clean results when folding cardboard. This is because without the grooves incorporated, it is very difficult to define a fold line. In the worst case, even the upper layers would tear completely.
Creasing is a forming process that is used in particular for paper, board or cardboard with higher grammages. In order to work the creases into the base material, it passes through the so-called creasing tool. Here, two different types of tools are available: vertically operating punching creasing tools and rotating rotary creasing tools.
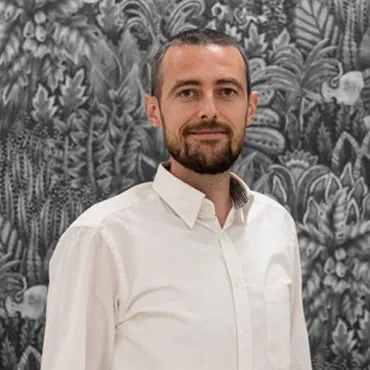
Product Advisor for Shipping Boxes
Whether it’s a simple folding box or a maxi letter box with adhesive strips – I’m your advisor for shipping boxes made from corrugated cardboard. Our printed packaging and inlays provide protection for products across almost all industries.
"Security and design? Corrugated cardboard offers both!"
I will be happy to help you personally.
Discover our printed boxes for corporate clients
Rotary creasing tools and die-cutting creasing tools: the biggest differences
The differences between these two variants can be clearly explained in the context of various printing processes. Which technique is used depends decisively on the process in question.
Creasing for printed products in the offset process
If the corresponding product is manufactured in the offset process, the majority of companies use rotary creasing tools. A characteristic feature of tools of this type is their angular shape. The creases are created by rotating blades. The entire creasing process must be closely monitored here, as the rotating creasing tools can damage the surface of the material.
This variant is particularly suitable for processing larger quantities or runs, as the tool can process the material quickly and thus also economically.
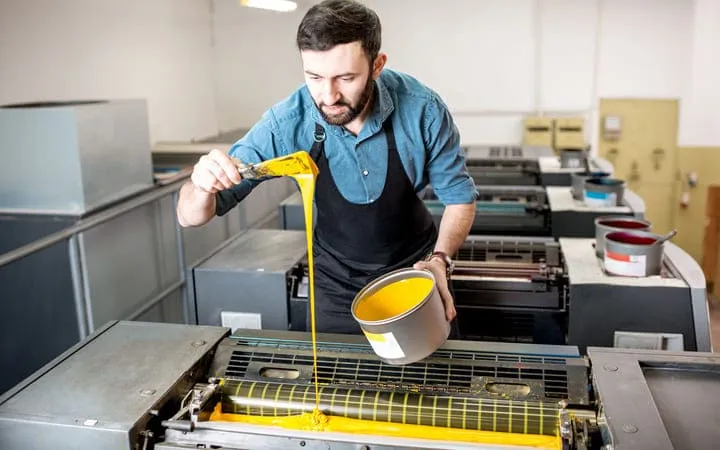
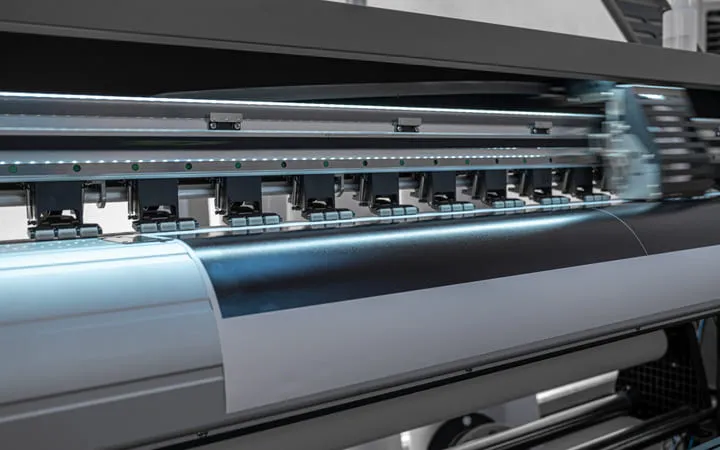
Creasing of printed products in the digital printing process
Depending on the type of digital printing process, the printed surface is somewhat more sensitive compared to the offset process. If rotary creasing tools are used here, this can lead to damage to the material. For this reason, the processing companies use punching creasing tools for this purpose. These are rounded on the sides so that they process printed surfaces much more gently than rotary creasing tools. Most tools of this type are equipped with so-called creasing bars, which crease the fixed material.
In terms of hourly output, the entire process takes considerably longer than when working with rotary creasing tools, but offers higher quality.
How are creasing tools constructed?
Although creasing tools usually have the same structure, they sometimes have design differences. The most commonly used tools have a thin, smooth edge on the punch, which is attached to a steel bar at the bottom of the tool. This edge is called the creasing line or creasing blade. In order to absorb the pressing pressure, a groove is precisely machined into a hard and thin material as a counter pole.
This is the creasing die, alternatively also called the counter die. The creasing blade or creasing rule then presses the paper or cardboard resting on the die directly into the groove, which ultimately results in a permanent crease.
The choice of dies should be made carefully in terms of design and individual performance characteristics. There are sometimes large differences in quality here. As a rule, optimum creasing results cannot be achieved with inferior tools.
Creasing rules in various designs
The type of creasing rules or creasing blades used depends largely on the material to be processed. As with cutting rules, various designs and construction models are available here. The range of possibilities is wide and extends from flattened or chamfered variants to creasing rules with reduced rounding. In practice, three basic types in particular have proven themselves and become established accordingly:
1. Standard creasing line for single flute corrugated board and paperboard
Standard creasing rule for single flute corrugated board and cardboard. This variant is characterized by a narrow base and a wide head. The width of the creasing rule can vary and depends primarily on the material thickness.
Example: If the cardboard thickness is between 0.20 and 0.35 mm, a creasing rule width of 0.5 mm is recommended. If, on the other hand, the cardboard thickness is in the range 0.85 to 1.10 mm, the width of the creasing rule should be 1.42 mm.
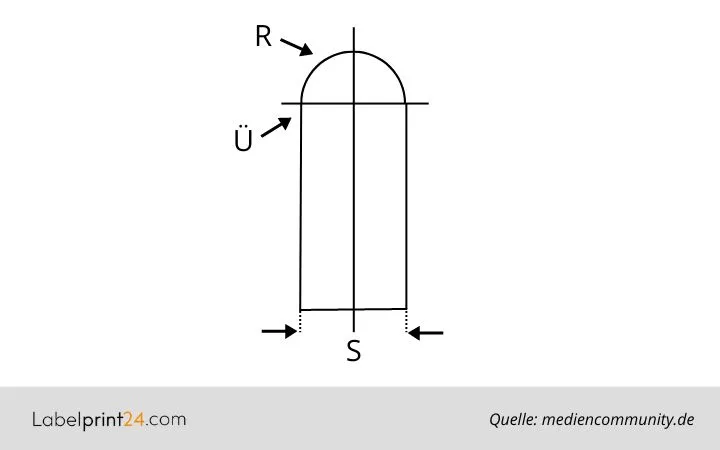
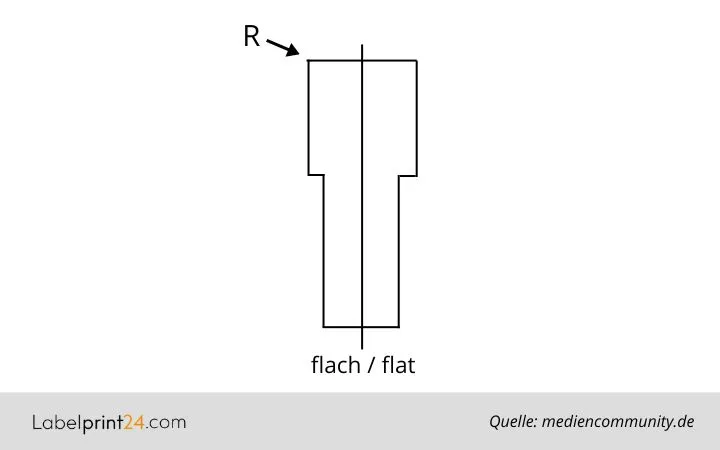
2. Head creaser with flat head
This type is primarily used for processing double-flute corrugated board. Sometimes this variant is also used for creasing 180° fold lines on single wall corrugated board.
Characteristic for a head creaser with flat head is the wide shaping and smaller cuts. Another advantage is that the head and base body can be quickly exchanged for components with other dimensions.
3. Head creaser with round head
These models are also mainly used for creasing corrugated board. There are no major differences to a head creaser with a flat head. In practical use, however, some users get along better with this variant.
.jpg)
In which cases is creasing recommended?
In general, creasing is used for classic print products, such as foldable cards, folding sheets and booklets. However, folding boxes, envelopes or folders also undergo a creasing process. This prevents paper breakage during subsequent folding.
Whether creasing is necessary always depends on the material volume and the respective grammage. The following applies here: the higher the volume of the material, the more compulsory the corresponding creasing steps are.
From a grammage of 180 g/m², creasing is mandatory.
A grammage of 180 g/m² represents a kind of limit value here. If the grammage of the material falls below this value, the material does not necessarily have to go through the creasing process. For paper, cardboard or board with a grammage of over 180 g/m², on the other hand, creasing is a must if the material is to be folded cleanly later.
In the case of cardboard or paperboard with grammages of more than 600 g/m², it is generally necessary to score or alternatively score the substrate several times before folding. The ratio between the creasing depth and creasing width is a decisive aspect for optimally realized creasing.
Creasing is mainly used in the packaging industry for the production of cardboard boxes and folding cartons or packaging - to facilitate setting up (manually or by machine). Booklets of books are also creased in the course of the manufacturing process. This makes it easier for readers to open the booklet cover later.
In addition, creasing is a prerequisite for folding print products in the first place. This is because the process prevents the materials or even the printed inks from breaking or bursting at the respective folding points. Folded and thus previously creased products include folders, multi-page postcards and business cards.
How creasing works in industrial practice
Two tools are always required for creasing. While the positive tool is located above the cardboard or paper to be creased, the negative tool is placed below this point. The material is then pressed against the negative tool on the underside. During the actual creasing process, the die with the integrated creasing lines moves continuously up and down above the carton.
A new crease is created with each downward movement. Extreme precision is required here. For the best possible quality, it is therefore crucial that the cardboard thickness, die thickness, groove width and the thickness of the creasing blade are always matched to each other in the best possible way for processing. Basically, every type of cardboard or corrugated board requires an individual die geometry to ensure really good working results.
For corrugated board, an alternative approach can be taken
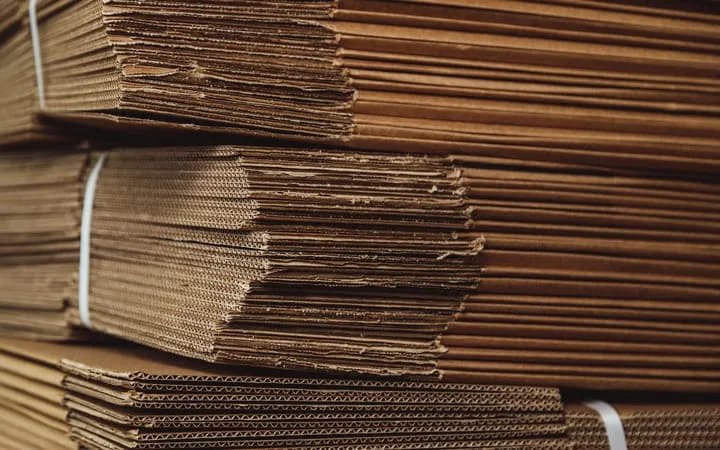
The creasing bars or lines of the tool create linear depressions on one side (on the flat blank) and a bead-like elevation in the form of a permanent deformation on the opposite side, which is created by the channel-shaped counter-creasing device. The creasing thus also defines the position of the fold line on a folding carton or on a folding box.
With the multilayer structure of corrugated board, special requirements arise. Here, no channel-shaped counter-creasing device is required. Therefore, the tool positioned at the bottom can be dispensed with. As a rule, it is sufficient for the creasing rule of the positive die to be pressed against a counter die plate.
In the industrial sector, the hollow groove is preferably used
However, there is another difference. For example, corrugated board materials are creased on the top inner side, while the creasing of cardboard is carried out on the print side. This ensures that the bead created by the creasing is on the inside. This is important for the subsequent folding process.
In the process, a distinction is also made between full creasing and hollow creasing. In the former case, pressing is performed on the complete surface. In contrast, in the case of hollow creasing, pressing is restricted to two edges only. This variant is also preferred in the industrial sector.